EV業界の協働ロボット
1. EV業界の協働ロボットの概要
1-1. 協働ロボットとは
協働ロボットとは、安全機能を内蔵し、ある条件を満たすことで人と同じ空間で稼働させることができる産業用ロボットの一種である。省スペースに設置ができ、プログラミングが容易でロボット未経験者でも短期間に操作方法を習得できるという特長も相まって、従来の産業用ロボットでは自動化が困難だった用途や環境でも利活用することができる。自動車や電機電子をはじめとしたさまざまな業界で人手不足対策、生産性向上や品質改善の手段として導入が進められている。
1-2. 協働ロボットの登場
協働ロボットが登場したのは2008年であるが、その背景については産業用ロボットの安全性に関する経緯を振り返る必要がある。1960年代に実用化された従来の産業用ロボットは1970年代以降に普及が急拡大したが、不十分な安全対策により事故の発生件数も増加したため、日本では労働災害を防止する目的で1983年に新たな安全規則が定められた。
まず、労働安全衛生規則 第150条の4において「産業用ロボットを運転する場合で労働者に危険が生ずるおそれのあるときには、さく又は囲いを設ける等の措置を行わなければならない」と定められた。同時に、労働省告示第51号により「80Wを超える駆動用原動機を有する機械は産業用ロボット」であることが明確化された(通称80W規制)。
これらの規則により、産業用ロボットの運転は安全柵で人と隔離することが必要となり、結果として人と産業用ロボットの協働作業を厳しく制限することになった。
2. 協働ロボットの普及
2-1.自動車業界における協働ロボット
自動車業界においては、重量物の搬送・組立、溶接や塗装といった身体への負荷が高く自動化による生産性および品質向上の効果が大きい用途を中心に産業用ロボットの導入が進められたが、一方で繊細な作業であったり、スペースや多品種対応が課題で自動化が進まない工程は人に頼ることが一般的であった。
2-2.協働ロボットの規制緩和
産業用ロボットを取り巻く安全規則は2013年に転機を迎えた。基発1224第2号通達によって規制緩和がなされ、後述する安全規格に適合した産業用ロボットおよびそのシステムは、ISO 12100に記載されたリスクアセスメントに基づく保護方策を実施して適切にリスクを低減することで、安全柵で囲って人と隔離することなく、人と同じ空間で稼働させることが可能になった。こうして「協働ロボット」は普及していく。
この規制緩和の背景には、技術革新が進み、欧米を中心に協働ロボットの導入が既に始まっていたという実績が考慮されたことが考えられる。
3. 協働ロボットの導入
3-1. 協働ロボット導入・成功例
世界で初めて協働ロボットを生産用に導入した企業はデンマークにあるLinatex社であると言われている。工業用のプラスチックおよびゴム製品のメーカーであるLinatex社は、2008年にユニバーサルロボット社から5kg可搬のUR5を導入し、CNC加工機へのロード・アンロード作業を自動化した。前例のないケースであったにもかかわらず、同社はロボットを安全柵で囲わず限られたスペースへ設置し、さらにプログラミングは社内のロボット未経験の人間が行うことに成功し、まさに協働ロボットの特長を体現するようなケースを作ってみせた。
3-2. 協働ロボット市場の今後
2008年に最初の1台が販売されて以来、協働ロボット市場は急速に成長している。2023年9月に公開された国際ロボット連盟(IFR)のレポートによると、2022年には産業用ロボット市場における協働ロボットの割合は販売台数ベースで全体の約10%に到達した。今後の見通しとしてはさまざまな調査会社がレポートを作成しているが、多くの場合で二桁の市場成長率を維持するものと見られている。例えば、2024年2月に日経BP社が発行した「ロボット未来予測2023」によると、協働ロボットの世界市場は2021年の1269億円から、33年には2兆9727億円に達するとの予測がなされている。
4. 協働ロボットの安全性
4-1. 協働ロボットの安全規格
協働ロボットが適合すべき個別機械安全規格(タイプC規格)として、ISO 10218-1/2および技術仕様書ISO/TS 15066が存在する。ISO 10218-1 (JIS B 8433-1)はロボットに対して、ISO 10218-2 (JIS B 8433-2)はロボットシステムに対する安全要求事項を定めたもので、ISO/TS 15066(TS B 0033)は、特に協働ロボットシステムに対する補完的な要求事項およびガイダンスを定めたものである。
4-2. 安全規格( ISO 10218-1・ISO/TS 15066)
ISO 10218-1およびISO/TS 15066は、協働ロボットシステムに対して(1)安全適合監視停止(2)ハンドガイド(3)速度及び間隔の監視(4)本質的設計または制御による動力及び力の制限、の4つのうち1つ以上に適合する必要があり、これらの機能の制御システムの安全関連部は、ISO 13849-1で規定するカテゴリ 3 のアーキテクチャでの PL=d、又はIEC 62061で規定するプルーフテスト間隔が 20 年以上、ハードウェアフォールトトレランスが 1 の SIL2に適合するように設計しなければならない、と要求している。
一般的に協働ロボットと呼ばれるものは(4)動力及び力の制限により、人や外部との接触を検知して安全に停止する機能を有している。この外力を検知するためのロボットの設計や制御方法はメーカーによってさまざまであるが、一般的にはアームの関節部に組み込まれたトルクセンサ等の機器によって外力を検出(入力)し、あらかじめ設定されたしきい値を超えたと判断された(論理)場合に、ロボットの動作を停止させる(出力)方法が挙げられる。
この入力・論理・出力といった一連の安全制御システムは、単一原因による故障で機能が損なわれてはならないというのがISO 10218-1 で定められているため、例えば冗長化された回路でこのシステムを構築することが必要となる。
また、ISO/TS 15066 ではロボットと人の接触に関する具体的なガイドラインが示されている。ロボットと人間の接触時間の違いによって「過渡的接触: 接触時間が0.5秒以下の衝突」と「準静的接触: 接触時間が0.5秒以上の押しつぶし状態」の2種類の接触の分類があり、この2種類の分類ごとに、さらに人の身体部位別でどこまでの接触力を許容できるかというガイドラインが示されている。協働ロボットと人を共有空間内で導入する際は、このガイドラインに従い、前述のISO 12100に記載されたリスクアセスメントを実施することが求められる。
5. 協働ロボットの種類
5-1. 垂直多関節型(単腕/双腕)
協働ロボットの種類としては、垂直多関節型で単腕または双腕タイプが実用化されている。単腕の垂直多関節ロボットとしては、6軸タイプが主流であるが一部7軸タイプも投入されている。
5-2. 垂直多関節(6軸タイプ)
6軸タイプを中心に取り上げると、主に可搬重量やアームの長さの違いによって各社から複数のラインナップが提供されており、一般的には可搬重量が大きくなるにつれてロボットのリーチも長くなる傾向にある。それ以外の違いとして、制御用の力覚センサを標準搭載したものや、カメラを標準搭載したタイプもある。
5-3. 各メーカー:安全性の違い
肝心の安全機能に関しては、力や速度の制限に対応するのは大前提として、各社によって機能に違いがみられる。アーム可動範囲やツール方向を制限できる機能があるもの、セーフティレーザースキャナの入力により速度を減速、さらに停止させる段階的な制御ができるもの、監視停止後に即座に動作を再開できるもの、などが挙げられる。
また、これらの個別の安全機能の全てが前述のISO 10218-1 で要求されるカテゴリ3のアーキテクチャでPL=d のレベルを満たしているかどうかもメーカーによって違いがある。
6.産業用ロボットとの違い・協働ロボットの利点
産業用ロボット | 協働ロボット | |
---|---|---|
人との隔離 | 安全柵で囲う必要あり | リスクアセスメントにより安全を確認できれば安全柵不要 |
可搬重量 | 数kg~1000kg超もあり | ~30kg程度 |
動作速度 | 速い | 遅い(安全柵無しで人と協働作業させる場合) |
設置方法 | 周辺設備含めて固定設置、移設は困難 | 小型軽量で移設、再配置が容易 |
スペース | 周辺設備含めて大きなスペースを要する | 省スペース、既存設備のレイアウトを変えずに、または最小限の変更で導入可能 |
プログラミング | 長期間のトレーニングや経験を積んだ専門の技術者が担当し、多くの場合は社外へ外注 | 未経験者でも操作が容易なインターフェース、内製化も可能 |
フレキシブルさ | 稼働開始後の動作やレイアウトの変更は困難かつ高コスト | 稼働開始後も柔軟に動作やツール、設置場所の変更が可能 |
自動化の範囲 | ライン丸ごと、または複数工程をまとめて | ラインの一部、特定作業のみの自動化が可能 |
自動化の対象 | 少品種、大量生産 人にはできない重量物搬送、高速作業、危険作業 |
多品種、小ロット生産 人が行う単純作業が中心、昨今では20kg前後の重量物搬送や、溶接・研磨など身体への負荷の高い作業への適用も |
6-1. コンパクトでフレキシブル
協働ロボットの利点はなんといってもコンパクトでフレキシブルな導入・運用が可能であるという点である。従来の産業用ロボットの場合、ロボットシステム全体は安全柵で囲い、人との協働作業はできないため、ある作業の前後の投入・排出といった工程も合わせて装置化する必要があるため、ロボットシステムが大規模になることが多く、導入後にそのレイアウトを変えることは現実的には極めて困難である。
6-2.容易なセットアップと運用
協働ロボットのプログラミングは専門の業者が行うためロボットの動作を変更する際は、外注または技能を習得した一部のエンジニアが担うことになる。一方協働ロボットであれば、安全柵無しで人との協働が可能なため、最初から工程を丸ごと自動化する必要が無いので、例えば最初は工程の一部のみ自動化して前後は人が作業をする構成にし、順次自動化の範囲を拡張するような導入ができる。システムが比較的コンパクトなため、セットアップに要する時間も短縮できる。運用時においては、プログラミングが容易なので社内でも修正ができ、軽量なので移動台車に設置して配置変更をしながら人による作業とロボットによる自動化を時間によって切り替えることもできる。
7. 協働ロボットの課題・解決策
7-1. 可搬重量・動作速度
協働ロボットの欠点は可搬重量が低いことと、動作速度が遅いことが挙げられる。これらは安全性とのトレードオフになるため容易に解決できない問題である。人とロボットの接触による衝撃力(運動量F)は、ワーク含めたロボット質量(m)と衝突時の速度(v)の積で求められる(F = m v)ため、単純に考えて重量物を高速で動かすシステムの衝撃力は大きくなり、安全ではなくなるためである。
7-2. 解決策
協働ロボットの課題(可搬重量が低いことと、動作速度が遅いこと)を解決するために、例えば本体が軽量なロボットを選択したり、エリアセンサ等を接続して人の接近により動作速度を落とす安全機能を備えているロボットを使うことが考えられる。
8. 自動車業界への協働ロボット導入
協働ロボットの導入が最も進んでいる業界のひとつが自動車である。省スペース、容易なセットアップ、協働作業空間の実現によるバックアップ要員の最適化が利点として評価され、従来の産業用ロボットでは自動化ができなかった作業に適用されている。
導入工程は多岐にわたり、パワートレインの加工・組立工程、車両組立工程におけるさまざまな作業用途に適用されている。一例として、加工機や検査機といった装置へのワーク投入・取り出し、エンジン・ギヤボックス・シリンダーブロックのねじ締め、エンジンへのオイル充填やリークテスト、ドアへのブチル塗布および防水シート押し付け、車両へのねじ締め、ボディ隙間検査、防錆材塗布や仕上げ研磨といった用途に対して協働ロボットが導入されている。
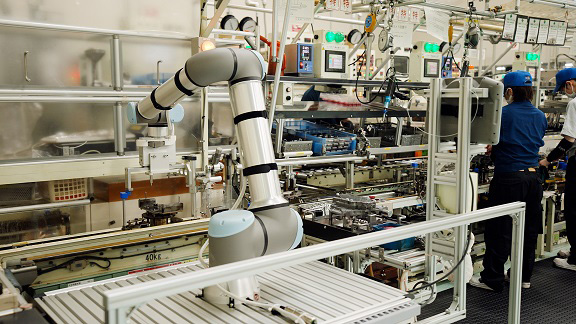
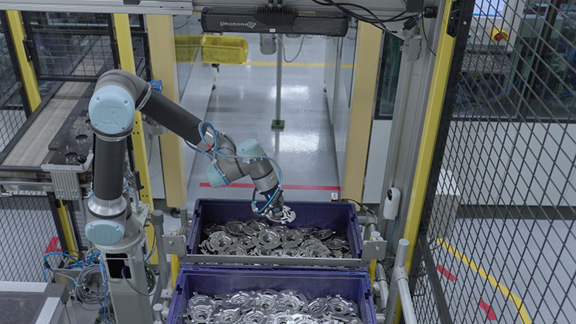
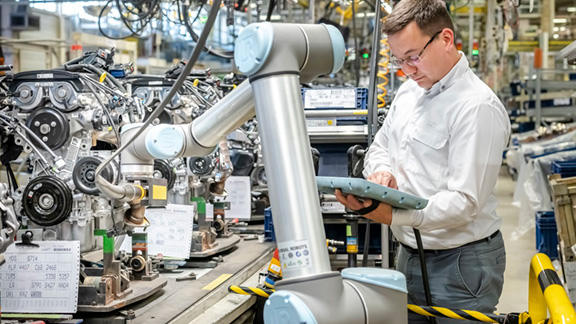
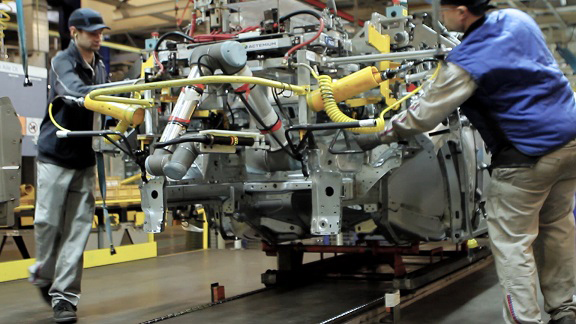
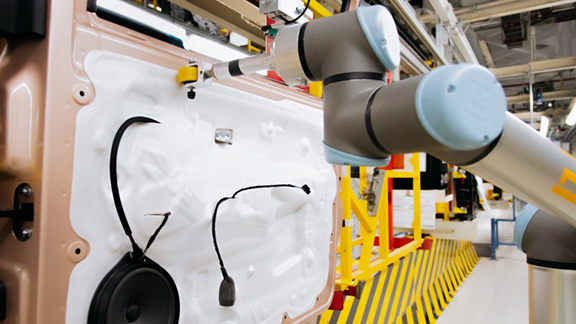
9. EV製造における協働ロボット導入
EV製造において協働ロボットが導入または検証されている例として、ここではバッテリー製造に焦点を当てて紹介する。セル・モジュール製造工程においては、各種装置間のハンドリング、検査機への投入・取り出し、通い箱等への箱詰め、シーリング材等の塗布、ねじ締め用途が挙げられる。ケース製造工程としては、AMRへ搭載した協働ロボットを用いてバッテリーケースの工程間搬送を行う例や、カメラを搭載した協働ロボットでケースの外観寸法検査を行う用途もある。バッテリーパック組立および車体組立工程においても、ねじ締めや検査作業が対象となる。EV市場全体で見ると、例えば充電ケーブルの挿抜作業の自動化を協働ロボットとAMRで行っている例も見られる。
10. 協働ロボット 今後の展望
今後の展望としては、EV市場がさらに拡大するにつれて、参入メーカーや車種が増えていくことが考えられる。車体の多様化に応じてバッテリーの品種も増加する上、バッテリーの技術革新も継続的に行われるため、バッテリーの製品ライフサイクルが短期化することも考えられる。それらに対応するため、需要に応じてフレキシブルに生産品目を切り替えられる工程が求められるようになり、例えばセル生産方式の採用が増えると、装置間・工程間搬送や組立工程を省スペースで柔軟にプログラミングができる協働ロボットの需要が増える可能性があり、協働ロボットを活用した合理化のテーマは今後も拡大していくことが見込まれる。
ユニバーサルロボットとしても、自動車製造工程において長年培ってきた実績を活かし、EV市場の発展のために世界中の顧客を今後もサポートしていく所存である。