機械設計用CADの概要
1.機械設計用CADとは
CADとは、設計や製図を支援するシステムソフトを指します。
機械設計用CADには大きく分けて2D-CADと3D-CADがあります。それぞれに特徴や得手不得手、その必然の元となる発展の歴史があります。乱暴な言い方をすれば、2D-CADは手書きの線画を清書するもの、3D-CADはコンピュータ上のデジタル空間に仮想製品を作るものと言えます。
手書き図面と比べると2D-CADは消しゴムの跡も残さずに修正できたり、何枚もきれいに印刷できたりと、図面流用がとても容易になりました。それでも2D図面を読み解くには製図ルールの理解と訓練が必要で、図面に馴染みの薄い方には正確に形状理解しづらいものでした。さらに訓練を受けた設計者でも他人が描いた大掛かりな組立図をすぐに理解するのはとても困難でした。
一方で3D-CADは見た目もわかりやすく、誰が見ても物の形状をすぐに理解できるようになりました。また2D図面は人間にしか理解できないためにコンピュータが直接演算したり編集したりすることはできませんでしたが、3Dモデルではコンピュータが直接モデル修正をしたり、様々な演算処理ができるようになりました。そのため、データ活用の広がりが桁違いに大きくなり、構造解析を使って強度計算や熱計算をしたり、物理シミュレーション、CGレンダリング作成等、様々な用途にデータを使いまわしたりすることができるようになりました。そしてパラメトリック機能を駆使すれば類似製品の自動設計も実現できるようになりました。
また2D-CADデータを自動で3D化することは困難ですが、3D-CADデータを2D図面化することはどの3D-CADでもできます。3D-CADを使えば製図ルールの理解が曖昧なままの初級設計者でもある程度の2D図面を作成できてしまいます。
このように3D-CADはメリットが多いのですが、落とし穴もあります。その数少ない欠点は、操作や概念が2D-CADと比較して大幅に複雑化してしまったことです。そのため自身の設計業務に合わない物を選ぶと運用に様々な問題が生じ、結果として2Dに後戻りしてしまいます。業務によって向き不向きが顕著となったため、2D-CADのように全社で同じCADに統一することが不可能となってしまいました。3D-CADを正しく選定するためにはその概念や用途、そしてその発展の歴史を多少なりとも理解する必要があります。
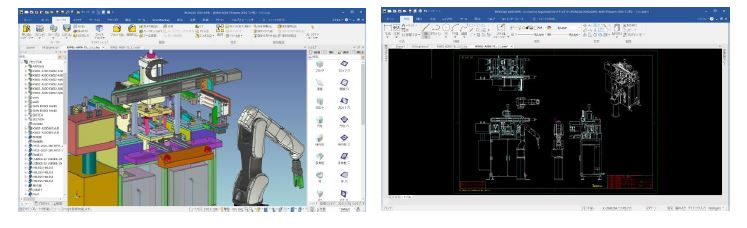
2.3D-CAD発展の歴史
初期の3D-CADのニーズは意匠面等の自由曲面の表現からでした。それはデザイン性が求められる自動車や家電製品等の金型を作るために必要で、その表現方法もハードウェアとソフト技術の進歩に合わせて、ワイヤーフレーム、サーフェス、ソリッドと発展していきました。
そして現在でも主流のソリッドモデルには当初は内部の演算誤差によるモデル破綻の問題がありました。演算処理できる小数点桁数の限度とそれに用いられる計算式が近似式であるため、演算処理を進めるにつれて内部誤差が増加し辻褄が合わなくなってしまうからです(一部のノンヒストリCADでは今でもその傾向が見られます)。
3.自動車業界でCADがどのように使用されているのか
自動車業界で使用されているCADの活用については大きく二分されています。それは自動車製品そのものとなる車体・部品等の量産製品設計分野と、それを作る生産技術としての装置・治具設計分野です。
量産製品設計分野
この分野では開発設計の段階で様々な検証が必要であるため、解析や検証機能等が充実しているハイエンドCADが主に使用されています。そして最上流の設計部門で作成された製品3Dデータは若干の加工を経て別業務用のデータとしてとことん使いまわすことができます。製造指示や文書向けの2D図面、金型用等加工のためのCAM用途、強度解析等のCAE用途、取説・パンフレット・広告等のCG用途等です。
今日ではどのメーカーもハイエンドCAD→PLM→その他基幹システム、といったデータの流れができており、一定レベルのDX化は10年以上前に実現していると言えます。今後しばらくは製品設計分野のCADにおける大幅な革新は起こりにくいと思われます。
生産技術分野における装置・治具設計
いわゆる一品物の製造装置・治具設計が主体で、一般的には2D-CADや限定的にミッドレンジ3D-CADを使用していることがほとんどです。
この分野では大幅な構造変更を伴う構想設計(トップダウン設計)が主流であるため拘束条件の厳しいパラメトリック系CADは不向きであり、互換性のためとはいえ、開発設計と同じハイエンドCADを利用するのは無理があります。
一部のトップメーカーのさらにごく一部の領域では生産技術分野でもフル3D化と図面レスを実現している所もありますが、CADと周辺システムを高度にカスタマイズできる技術力と資金力とを兼ね備えたトップ企業ならではの特殊事例であり、業界一般に普及するのはまだまだ先です。他の多くの完成車メーカーや部品メーカーでは未だに生産技術分野の3D化の遅れが問題となっています。
今後はDXやIoTの革新を起こす第一歩として生産技術分野の3D化が必須になるため、この問題の解決が急務となっています。
ではどうしてこの二つの分野で3D化の格差が顕著になったのでしょうか?それは前述したCADの発展の歴史と各分野での設計業務のアプローチの違いに原因があります。
4.量産製品設計と生産技術分野の装置治具設計との違い
どちらも“機械設計”と一括りにされていますが、量産製品設計と一品物の機械装置・治具設計ではそのアプローチや考え方に大きな違いがあります。
量産製品設計 | 一品物の機械装置・治具設計 | |
---|---|---|
形状 | 自由曲面が多く含まれ、2Dでは表現しにくい。![]() |
板・円柱等の単純形状の組合せが多く、ほぼ2Dで表現できる。金型や受け治具で意匠面を正確に扱えるレベルでよい。![]() |
設計時間・設計計算量 |
・製品開発では解析や実験を繰り返すため、設計検証のために比較的時間をかけなければならない。最適形状、構造解析等の計算量、実験量が多い。 ・重量増がコストや性能に直結する。業務時間内でのCAD操作時間比率は比較的少ない。 ![]() |
・スピード重視で時間をかけられない。すぐに設計し、すぐに出図。「重量減らすより工数減らせ」、の考え方。 ・計算量・実験量ともに少ない。業務時間内でのCAD操作時間比率は比較的多い。 |
設計の内容 |
構造はおよそ決まっており、サイズ・形状設計が主体。 例:自動車エンジン設計であれば世界中、どこのメーカーでも4気筒レシプロエンジンの構造はほぼ同じである。ピストン、コンロッド、クランク、CYLヘッド、EGブロック等の構造自体はほぼ同じであり、サイズ(ボア・ストローク、排気量)や燃焼室形状、ピストンヘッド形状等によって馬力、トルク、燃費性能が変わってくる。 ![]() |
構造やレイアウトは決まっておらず、試行錯誤しながら構造ごと設計していく。 例:工程や動作に必要なモーターやシリンダー等のアクチュエーター等は市販品をそのままレイアウトし、それぞれを保持したりつないだりするブラケットやフレーム等を設計していく。前述したようにそれの部品は単純形状の集まりで、これら全体の構造や位置関係が重要な設計要素である。 ![]() |
設計の範囲 | 狭く、深く。 例:自動車のブレーキ担当者はとことんブレーキについての開発・設計を追求。また同時に別のエンジン部品設計等に携わることはない。 |
広く、浅く。 例:装置設計者は架台フレーム、搬送ユニット、クランプユニット、加工ユニット、検査ユニット、受け治具、カバー、安全装置等すべてを設計 |
業務体制 |
・1人の設計者が1つのユニット。図面枚数は比較的少ない。 ・ユニットや部品ごとに設計担当が分業化されている。車1台に関わる設計者は数百~千名規模。 ・CAD操作は専門のCADオペレータが実施することが多い。 |
・比較的分業化されておらず、1人の設計者が装置全体を設計することも多い。ライン物の装置でも数名以内。 ・1人あたりが描く図面枚数はかなり多い。 ・設計者自らがCADを操作。 |
データ互換・双方向性 | ・異なる部署、異なる企業であっても同じCADの同じバージョンを用いて双方向にネイティブデータをやりとり。 ・設計変更が頻繁に発生するため相互に修正が容易なネイティブデータでなければならない。 |
・中間ファイルや2D図で製品データを取り込んだあとは、それに合わせた治具や装置を作るのみで、製品データを修正することはない。そのため、製品データの流れは一方通行でよく、データ変換さえ上手くいけば異なるCADを使用しても問題とならない。 |
部品加工・検査 | ・3Dモデルを重視。金型や試作に3Dデータを活用。金型による成型加工が多い。 ・検査工程も自動化されていることが多い。 |
・設計後の部品加工は紙図面主体。 ・図面レスはまだまだ将来の課題。 ・加工も検査もまだまだ手作業が残っている。 |
5.これらの違いから生じる様々な問題
このように3D-CADは上記の量産製品設計向けのニーズで発展してきたために、従来の2D-CADとは概念や運用面で大きな違いが出てきました。この違いが一品物の装置・治具設計で3D-CADを運用する際のトラブルの元となるのです。量産製品設計では便利だった機能や概念が逆に仇となってしまったのです。
拘束条件、履歴の使いこなしの困難さ
フィーチャパラメトリック系CADの利点の一つは適切な拘束条件を付加しておけば、その数値を変えるだけで関連する箇所が自動的に変更されることですが、それを実現させるには高度なモデリング技術が必要となってきます。また、構造が大幅に変わる場合は拘束条件が通用しなくなることが多く、変更によってはモデルが破綻するトラブルも発生します。この利点が活かされるのは構造があまり変わらない量産製品設計分野だけとなります。
トップダウン設計・ボトムアップ設計の違い
ほとんどの3D-CADでは、従来の2Dトップダウン設計の流れであった、「ポンチ絵→構想図→組立図→部品図バラシ」のステップがやりにくくなっています。2D-CADにおいては組立図までの作業を一つの図面ファイルで行い、部品図バラシ作業の段階で初めてファイルの切り分けをしていました。ところが多くの3D-CADではパーツファイルとアセンブリファイルの拡張子が分かれており、パーツを作る際にはその受け皿となるパーツファイルを先に準備作成し、それをアセンブリファイルに集めて組み立てるボトムアップ設計の流れが一般的です。
装置設計の初期段階では、どんな構造になるのか、どんな部品が必要なのかがわからない状態であり、それをこれから考えていくのが仕事なのですが、多くの3D-CADでは最終工程であった部品図バラシを先にしなければならないという大きな矛盾が発生してしまうのです。
データ流用性・互換性の問題
2D-CADは他のCADで書かれた図形もDXF変換すれば自身のCADで編集・流用することが容易でした。ところが3D-CADでは中間ファイルに変換すると元の履歴やフィーチャ情報は消えてしまい、編集できなくなってしまいます。またほとんどの3D-CADは後方互換しか持たないため、同じCADでも別の企業間等でバージョンが異なるとデータ流用が困難になってしまいます。
またデータ変換も要注意で、3D-CADでは適切なフォーマットと設定を選択しないとデータの崩れが頻発します。それぞれのCADで使われているモデリングカーネルやトランスレータによっても相性や変換性能が変わり、これが悪いとデータ変換処理や修正作業の工数が膨大となって作業がまったく先に進まないこともあります。
付属の2D-CADが使いにくいという問題
3D-CADはあくまでも3D主体で開発されており、付属の2D-CADはオマケ程度のものも少なくありません。ある程度の2D設計作業をするためには別途2D-CADを準備する必要があります。また従来使い慣れている2D-CADとは異なるメーカーへ移行する場合、3Dのみならず新しい2Dの操作も覚えなければならないことも注意が必要です。
このように生産技術分野の業務に量産製品設計向けの3D-CADを選択することが3D化失敗のほとんどの原因なのです。その結果、2D-CADから抜け出せない、2Dに慣れたベテランが使ってくれない、プレゼン用のモデリングにしか使えない、ゼロからの構想設計ができない、2Dよりも多大な工数がかかってしまう、等のトラブルが発生してしまうのです。
6.IRONCADの紹介
株式会社クリエイティブマシンの販売するIRONCADは、生産技術分野における3D化推進のトラブルを下記の特徴によってすべて解消している唯一の3D-CADです。
簡単モデリング
スケッチも拘束もいらない、まるで粘土と積木のような操作性で素早くモデリングできます。ヒストリ系・ノンヒストリ系の良いとこ取りをしたフィーチャベースのダイレクトモデリングです。もちろん、スケッチ&押出しやサーフェス等の複雑形状のモデリングもできます。
簡単アセンブリ
シンプルでわかりやすいグループ階層化アセンブリ機能で拘束を極力使わずにアセンブリできます。
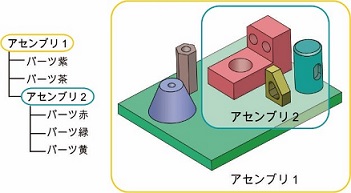
位置決めも拘束を使わずに専用3D移動ツールの「トライボール」で簡単です。
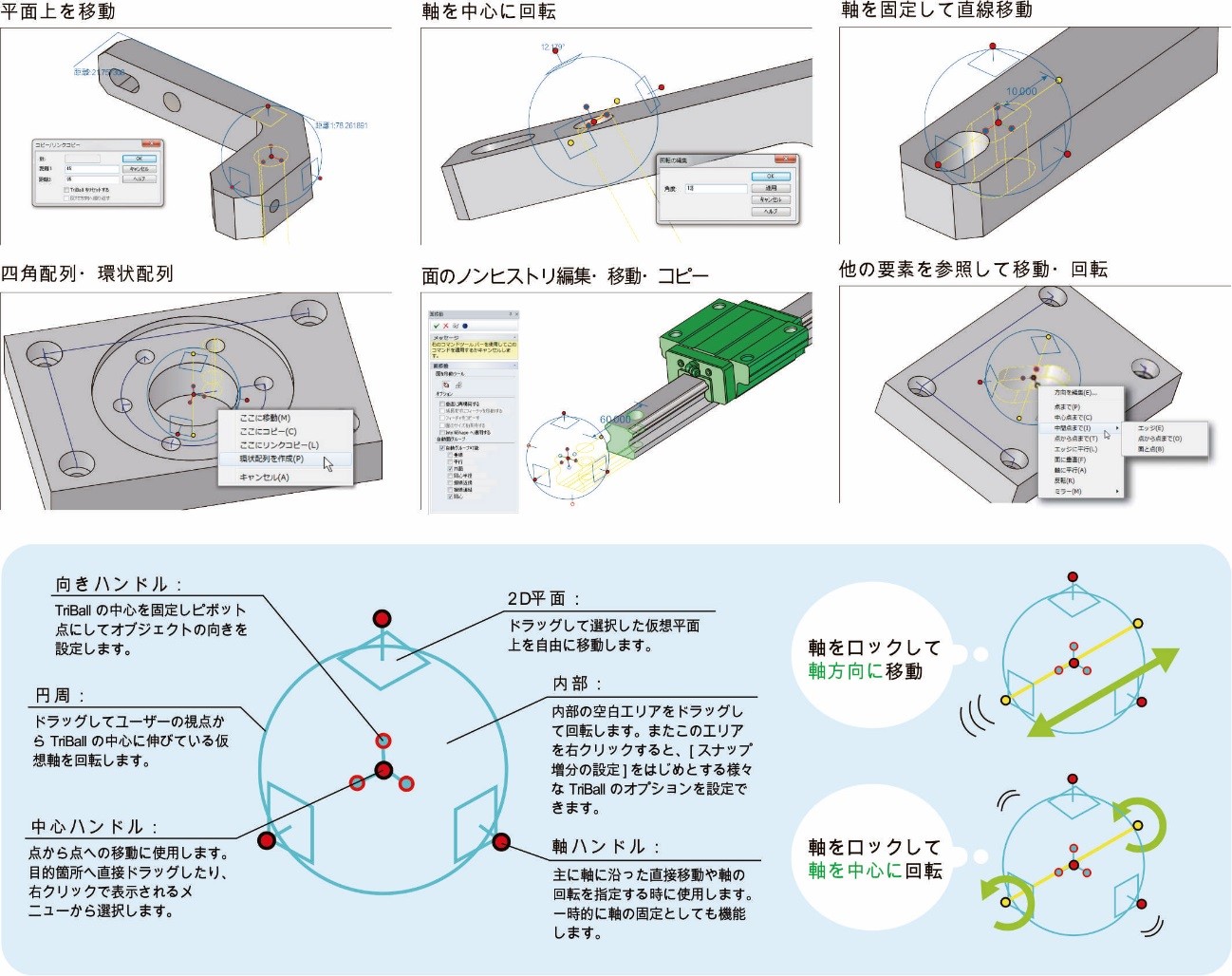
構想に便利なデータ構造
ファイル拡張子が1種類のみで、アセンブリとしてもパーツとしても保存できます。一つのアセンブリファイルにいくつものサブアセンブリやパーツを内包でき、それらを自由に好きなタイミングで外部リンク保存したりリンク解除したりできます。3Dでありながら2D時代の「ポンチ絵→構想図→組立図→部品図バラシ」のステップが容易です。
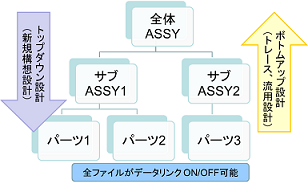
高速レスポンス
大規模アセンブリモデルの取り扱いも軽快で、バージョンごとに改善させています。64ビットネイティブであるため、将来も安心です。
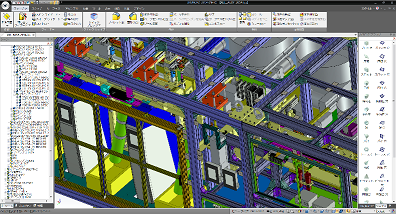
高いデータ互換性
業界唯一、Parasolid、ACISのデュアルカーネル搭載し、世の中の多くのCADとカーネルネイティブでのデータ変換が可能でデータ変換のトラブルも減少しています。設計上流からのデータ取り込みも協力企業とのやり取りも容易です。
高いデータ流用性
フィーチャの無くなった他CADファイルもノンヒストリ機能で編集可能です。
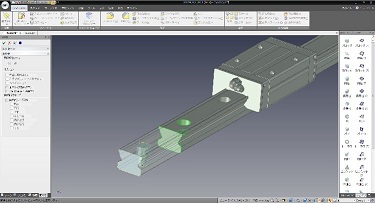
2D設計も違和感無し
DWG互換の2D-CADを搭載しており、本格的な2D設計も従来通り可能です。操作方法も他のDWG系CADと同じなので、場合によっては習得期間も無しで済みます。
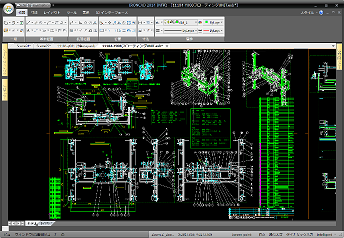
豊富なオプション機能
CAE、ロボットシミュレータ、業界唯一の自動2D→3D生成アドイン等、生産技術分野で必要な機能を揃えています。
モデリングスピードのベンチマークではどの他社CADよりも早く、いずれも1/2以下の工数でした。CADを代えるだけで確実に設計工数を減らすことができるのです。この点でも、常に仕事のスピードが求められる自動車業界の生産技術分野においてこのCADがマッチしているといえるでしょう。
昨今ではDXをはじめ、IoT、デジタルツイン、スマートファクトリー等の言葉が聞かれますが、いずれも生産技術分野の3次元化が前提条件となっています。3次元化でつまずいていると感じているメーカー様はぜひIRONCADをご検討いただきたいと思います。