自動車向け軽量化技術とは
1. 自動車向け軽量化技術の概要
自動車産業では、燃費の向上や環境負荷の軽減、さらには加減速やハンドリングなどの走行性能の向上のため、車体の軽量化が重要なテーマとなっている。軽量化技術の進展は、電気自動車(EV)やハイブリッド車においても、航続距離の延長やバッテリー効率の向上に寄与している。
軽量化の手法の一つは素材自体を変えることにあり、鉄の比重=7.8に対して、アルミの比重=2.7、樹脂の比重=0.9~1.4であることからも、出来ることなら樹脂化することがベストな選択と言ってよい。自動車の樹脂化は、既に多くの部品で広く採用されており、外装(バンパー、フェンダー、ドアミラー)、内装(ダッシュボード、ドアトリム、センターコンソール)、エンジン周り(インテークマニホールド、エンジンカバー)、電装部品(バッテリーケース、ハーネス)、さらには燃料タンクまで、多岐にわたる部品に樹脂が使用され、技術の進歩とともにその適用範囲は拡大している。
2. 自動車向け軽量化技術 樹脂化によるメリット
樹脂化するメリットは軽量化に尽きる。比重の軽い樹脂素材を使用することで、自動車の総重量を大幅に軽減でき、走行に必要なエネルギーも軽減できるため、燃費向上や二酸化炭素排出量の削減に繋がる。また、複数の部品を一つにまとめて一体化することで、一回で成形でき、かつ、大量に生産できるため生産コストの削減が可能となり、デザインの自由度も広がる。
しかしながら樹脂化に至らない部品が存在するのは、設計者を悩ませる樹脂特有の課題、例えば肉厚が均一になるように設計しなければならないなど、樹脂設計における基本的な概念が邪魔をしている。ここでは「ガスインジェクション」という技法によって、解決した事例などを紹介していきたいと思う。
3. 自動車向け軽量化技術としてガスインジェクション技法を紹介
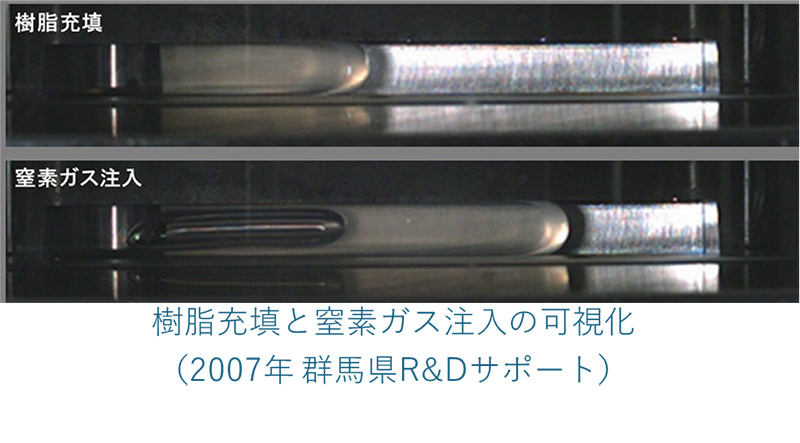
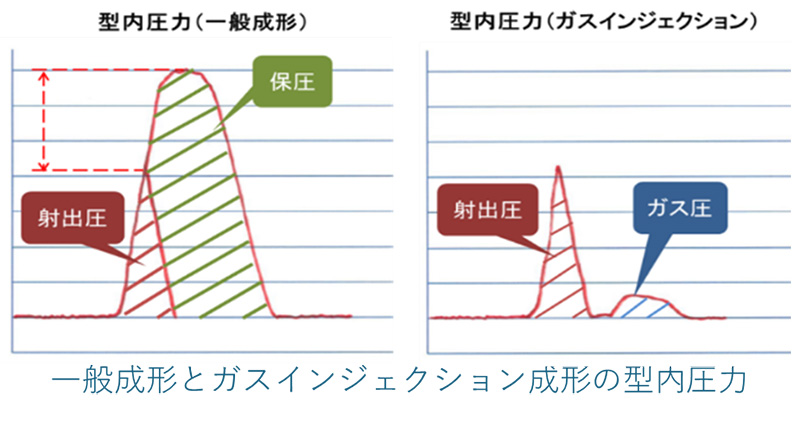
一般の射出成形では金型に樹脂を充填した後に樹脂が冷却固化するまで保圧(高圧)を数秒間かけて形成する。が、ガスインジェクション製法では金型に樹脂を充填した後、窒素ガスを注入して製品内部から圧力(低圧)を保持する仕組みで、金型内の圧力を低圧に保つことが出来る。これにより成形機のダウンサイジングが可能になり、コストダウンに貢献できる。さらに一般成形の欠点であったヒケ・ソリ・バリ等の外観不良を改善し、寸法精度を向上するなどメリットの多い成形方法と言える。
しかしながら、射出成形メーカーの中でもガスインジェクション技術を保有するメーカーが1%程度しか存在しないのは、高額な設備投資も必要になるが、それ以上に技術的ノウハウが重要、かつ、大きな壁となっているからである。
4. ガスインジェクション技法による樹脂化の用途
ガスインジェクション技法を用いて樹脂化した多くの採用事例の中から、課題を解決した事例をいくつかご紹介し、樹脂設計の常識や制限を、見直す機会となったら幸いなことである。
4-1. 強度確保
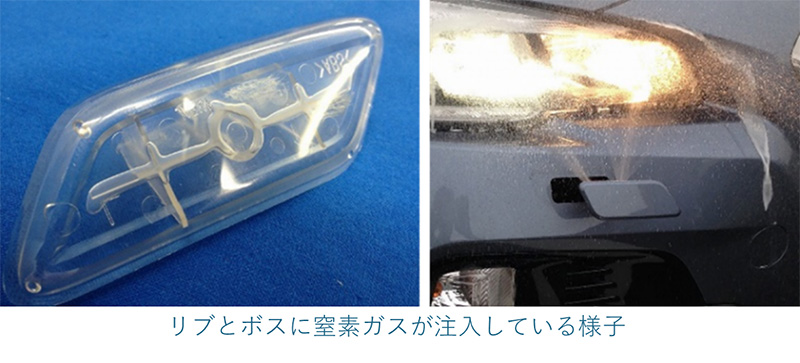
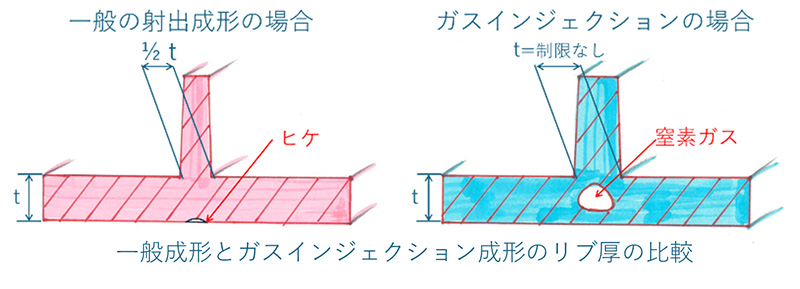
金属を樹脂化するうえで最も課題となるのが強度であり、樹脂製品の強度を確保するとき、製品裏側にリブやボスを設置して強度の維持を試みる。しかし、リブやボスを形成すると、表面側(外観側)にヒケ(くぼみ)が発生してしまう。
樹脂製品を設計する際、リブの根本の肉厚は天面の肉厚の1/2以下で設計するのが基本であり、ゲートの近くで圧力が伝えられるとしても2/3程度が限界とされている。さらにヒケを防ぐため樹脂圧力を過大に掛けることで変形も発生していた。
ガスインジェクション成形ならリブの根本に窒素ガスを導いて内部から保圧するためリブの肉厚に制限を必要としない。残留応力が無い低圧保持のため寸法(3次元形状)を忠実に再現しボディにフィットさせることができる。
4-2. 寸法精度(ソリ)
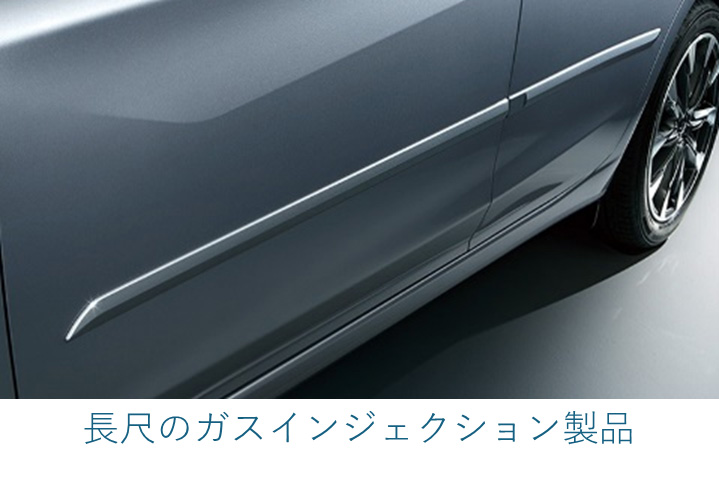
金属(鉄)の熱膨張係数(11.8×10-6/℃)に比べ樹脂の熱膨張係数(65~140×10-6/℃)からしてみても寸法変化は樹脂の方がはるかに大きい。が、仮に10℃変化してもマイクロレベルである。環境依存よりもむしろ樹脂成形時における分子配向や成形ひずみによる変形こそ寸法精度に悪影響をおよぼす要因である。ドアに貼り付けるサイドモールなど長尺の部品はソリが出やすく、はがれやすいなどの問題を生じていた。
ガスインジェクション技法においては、一般の射出成形の保圧工程(50~100MPa)を必要とせず、窒素ガスを注入して内部から低圧(10MPa程度)で、しかも製品の全領域で均等に保持するため、分子配向や成形ひずみはあまり考慮せずに、ソリのほとんどない長尺製品を形成することが出来る。さらに、樹脂流動のバラツキを注入した窒素ガスが緩和してくれるため、一度決めた条件でバラツキが極端に少ないのもガスインジェクション製品の特長である。
4-3. 偏肉構成
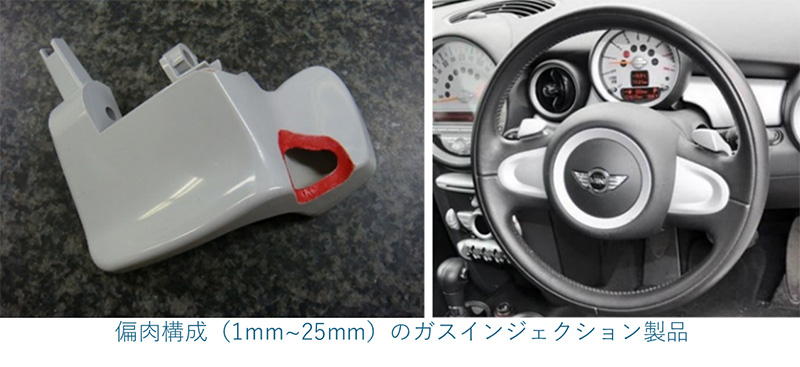
樹脂設計者やプロダクトデザイナーに最も喜ばれる効能を発揮するのが、偏肉構成でも形成可能なことである。薄肉1mm~厚肉25mmの混在した製品も形成することができる。
厚肉の部分に窒素ガスを注入することで、製品内部の圧力が均一化された製品となっている。ガスインジェクション技法でなければ形成不可能な製品と言える。通常では裏側に大きな肉抜きを形成しなければならないが、ご覧のとおりデザイン重視で形成した事例である。樹脂設計で基本中の基本とされる肉厚の均一化は無視していただいて結構だ。
4-4. 一体化
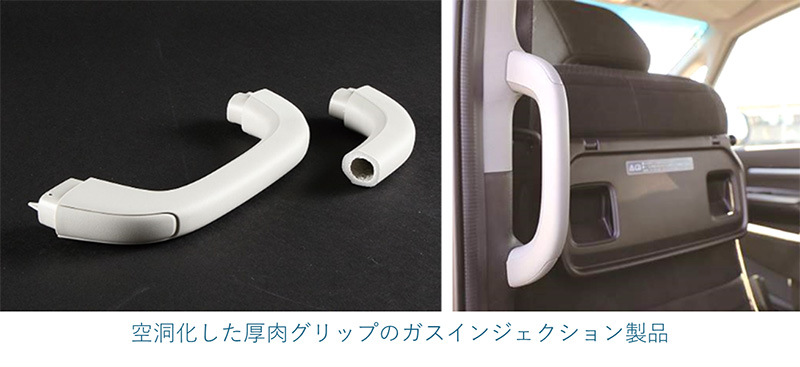
偏肉構成が可能であることから、複数の部品を一つにまとめて一回で成形することが可能となり、コストメリットを発揮することが出来る。車内用グリップでは、通常360秒の成形サイクルが必要であったが、中空構造にすることで冷却時間が大幅に短縮され、成形サイクルも60秒程度に短縮された。また、30%以上の軽量化を実現して、樹脂使用料の削減にもつながっている。
自動車内のグリップは、現在では、ほとんどガスインジェクション技法で形成されている。
4-5. 樹脂パイプ
パイプ類も金属製から樹脂化への流れにのって、着実に採用され始めている。金属製パイプの場合、曲げ加工・バルジ加工・ロウ付け・ビーディング・脱脂などの複数の工程により形成するが、樹脂パイプの場合ガスインジェクションによる空洞化および複数部品の一体化により1回で形成できるので、軽量化(70%削減)のみならず、工数削減によるコスト削減(70%削減)、リードタイム短縮が可能となる。
樹脂の材質も汎用樹脂からスーパーエンプラ、さらにエラストマーや生分解性プラスチックなど熱可塑性樹脂で対応可能だ。太さはΦ6~Φ30、長さは2mの範囲で実績があり、分岐管でも形成可能である。さらに、樹脂製パイプなら2層構成で形成することもでき、例えば内壁面には耐薬品性の樹脂で、外壁には強度保持用のガラスフィラー入り樹脂など、異なる機能を持たせることも可能である。
しかしながら、自動車のエンジンルーム内を設計する際、最後にパイプの配置が決まるため、金属パイプなら後から曲げたり設計変更することが出来た。しかし、樹脂製の場合、形状は金型で決定してしまうため、初期段階から設計上の十分な検討が必要である。
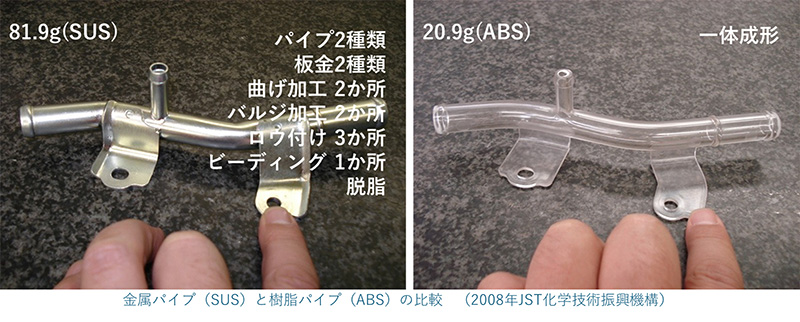
5. ガスインジェクションを得意とするジュンコーポレイションについて
株式会社ジュンコーポレイションは0(ゼロ)から1を生み出すことを喜びとして、その製法から検討し、必要であれば導入し、必要であれば自社で開発する。たいていの課題は、ガスインジェクション技法により解決できる場合が多い。1980年代後半から1990年代前半にガスインジェクションのブームが世界中で起こったが、その後もガスインジェクション技術の課題を克服し、磨き続けてきた。この開発の軌跡は経済産業省のサポインをはじめとする委託事業や自動車メーカーとの試作開発(ペダル類やワイパー、ドアミラー、樹脂パイプなど)の実績により、さらに高度化し、大きな信頼も得られている。
成形設備は50tonから350tonの射出成形機16台を保有し、全ての生産ラインでガスインジェクション対応している。ガスインジェクションに必要な高圧窒素ガス発生装置などの設備も独自に開発しており、他社を圧倒する。ぜひこの機会に「ガスインジェクション」についてご検討されてはみてはいかがでしょうか。
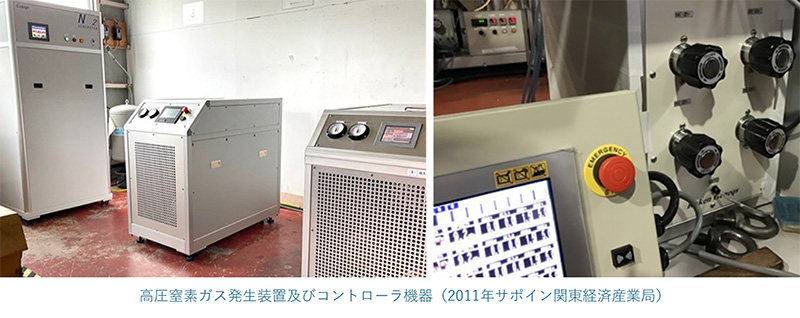
(著)株式会社ジュンコーポレイション